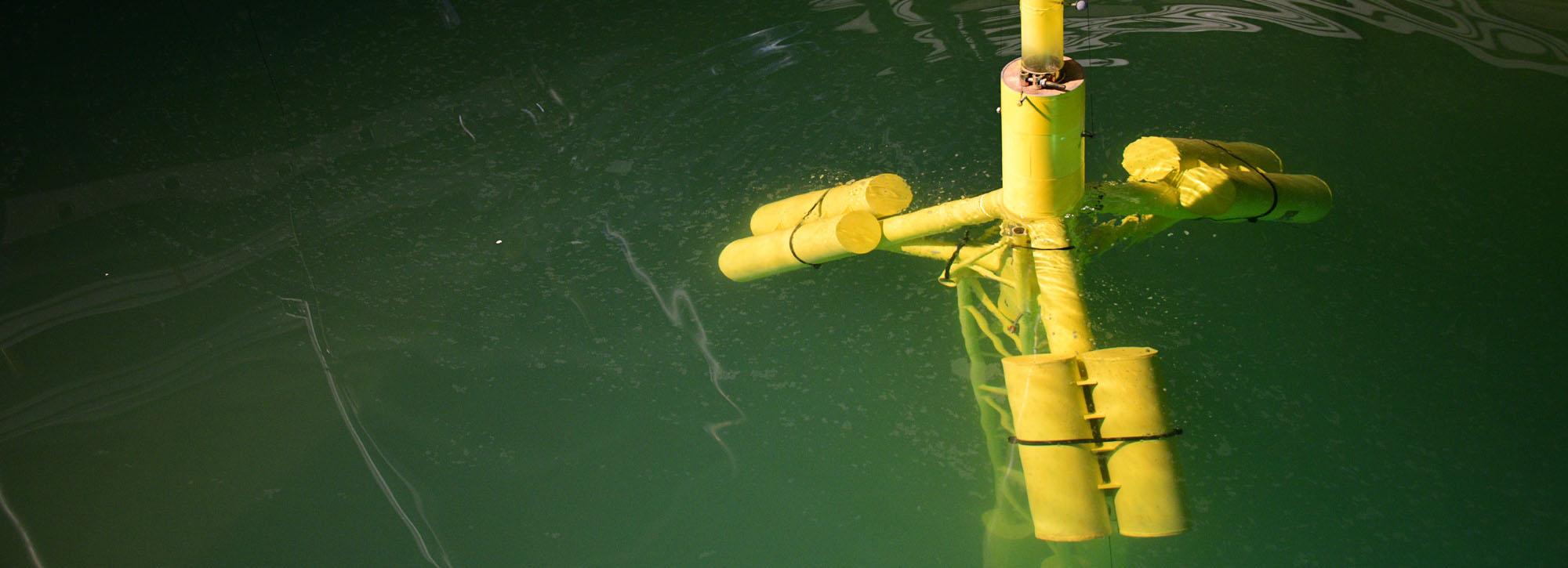
Deep knowledge to support floating turbines
As the offshore wind industry edges closer to installing large-scale floating wind farms, it’s crucial that designs are cost-effective and safe in deep seas. Mike Case, our lead for clean energy, examines how existing marine modelling knowhow can tackle technical challenges and help make these huge structures more affordable.
Floating wind power is on course to become an essential part of the renewables mix, as the additional power generated by installing turbines in deeper seas will be key in meeting carbon reduction targets. Small-scale installations have proved that floating wind works as a concept, and many countries are now seeking to ramp up their activities to the GW scale. For instance, the UK and Scottish governments announced substantial investments in floating wind projects last month.
Floating offshore wind offers the advantage over fixed bottom turbines of not needing a suitable continental shelf, making wind power an option for those countries without access to shallow waters. Even countries with suitable water depths for fixed bottom installations are finding that space is becoming constrained with competing interests from shipping, fishing, defence and increasing concerns over the cumulative ecological impacts of multiple large scale windfarms in close proximity to each other.
Another benefit of deep seas are that the winds there are typically stronger, less turbulent and more consistent, offering improved capacity factors. Larger turbines will also be possible as the visual impact from the coast will be much reduced due to the distance from shore.
Water-related challenges
However, deeper waters bring challenges with them. Wind turbine foundations and mooring systems need to cope with more extreme wave and hydrodynamic forces, and the turbines with stronger wind forces. Other challenges stem from the complexity of logistics due to the sheer size of the structures – for stability, semi-submersible foundations need to be similar in size to oil and gas platforms (~100m across), making them cumbersome to fabricate, transport, and install. We also need to understand the seabed related challenges of anchoring, dynamic inter-array and export cables and having tens of kms of catenary mooring chains moving on the seabed.
Not only do all these areas need analysing for safety and environmental impact, but also to help optimise the design in terms of cost of operation and construction. The size of these foundations makes them more expensive to build and install than their fixed bottom counterparts, and developers need to overcome significant engineering and logistical challenges to make giga-watt scale deployments cost-effective.
Modelling wave forces on the structure
Properly understanding and quantifying the wave forces is key to a successful engineering design – for affordability and safety. Modelling the performance of the structure to help optimise the design before construction begins is therefore crucial for cost savings.
Computational simulations can be used to analyse the wave pressures exerted on a foundation structure under a range of conditions. To calibrate and validate these numerical models, it is necessary to gather data on the structure’s behaviour by building a scale model and conducting physical tests in a wave flume. Hydraulic specialists can run tests in the flume for different wave conditions and wind directions.
The data gathered from physical and computational modelling are then used by engineers to perform further structural analysis and refine the design. Having determined the most efficient dimensions for the design, construction costs can be calculated, which in turn are fed into the levelized cost of energy.
We recently tested Floating Energy Systems’ foundation concept to help reduce risks and make it cost-effective. Engineers used physical (1:67 scale) and computational models to examine the Stinger Keel’s hydrodynamic performance as part of a one-year project funded by Innovate UK.
Our team developed two numerical models – an OpenFAST model and an OpenFOAM CFD (Computational Fluid Dynamic) model. The OpenFAST model looks more suitable at early design stages for calculating initial wave and hydrodynamic pressures on the structure. The CFD model is useful in advanced design stages for finetuning details. It can also be used for future design iterations, without the need for further physical testing, which will save time and money.
Watch our video testing the physical model of the Stinger Keel in our lab, alongside our numerical model
Effective mooring systems
As the turbines will be anchored to the seabed by mooring, understanding the water forces on them is also crucial. The aim is to attach the structure so that it moves as little as possible, optimising energy extraction efficiency.
Modelling can help ascertain the most effective mooring options, and we are running an internal research project with a special focus on the fully dynamic simulation of mooring lines. These can significantly affect station keeping and the overall response of the device. Once again, physical models can be used to test mooring configurations in order to validate and configure numerical models.
Protecting cabling on the seabed
The cables and cable protection systems, which transfer the power generated to shore, naturally present similar challenges as those for fixed bottom foundations. We have years of experience studying the movement of the seabed and how sedimentation move around cables for other sectors, but the offshore wind industry is still in its relative infancy, and a number of recent cable failures show there is still more to learn.
Installing the structures
The scale of the structures needed for floating offshore wind is also increasing the demand for port facilities with the right conditions and space for final assembly and marshalling, as well as to act as bases for operations and maintenance in the future. For example, it is projected that floating offshore wind construction will need ports with laydown areas of as much as 20 ha, quay lengths of 550m and water depths of up to 15m. Thus, in the areas where construction is concentrated, there may well be a shortage of port capacity. This is driving interest in potential expansion works that may be needed to support the growth in marine renewables.
With decades of experience in modelling, navigation, and feasibility studies at ports all around the UK coastline, we are already helping port operators plan the necessary upgrades to deliver the round-the-clock facilities at a proportionate cost.
Environmental considerations
The ramping-up of the floating offshore wind sector inevitably raises concerns over the environmental impacts of these new structures on the marine environment. At HR Wallingford we provide the independent scientific evidence to feed into environmental impact assessments of all kinds of marine infrastructure, and we expect floating offshore wind to be no exception.
For example, it’s important to understand the impact of underwater noise levels, particularly those generated during the construction phase, on the marine environment – on the seabed, and for other marine life such as dolphins, whales and fish.
With the marine renewables sector in mind, we have co-developed an underwater noise propagation model which predicts noise levels at distance from a point source. The tool can be used to investigate the impact of underwater noise propagation and how marine species behaviour may change as a result of this disturbance.
The supporting infrastructure for floating offshore wind, including the cable connections and the port infrastructure, also need to be assessed. We have the modelling tools to objectively determine the influence of these types of structure upon marine processes such as tides, waves and sediment movements. This evidence can then feed into the wider environmental impact process.
Instilling confidence
Although floating turbines raise new challenges for the offshore wind industry, it’s clear that there are solutions that can be re-purposed from other sectors. What is slightly different for floating wind is the sheer volume of turbines that are likely to be installed – we expect to see large-scale wind-farms in Europe and Asia being built in the next 5 to 10 years – but modelling undertaken by real experts offers a tried and tested route to instil confidence that designs will function effectively.
Want to know more?
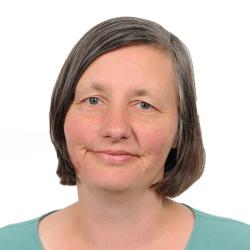